А. Оптимизация пятна застройки.
Очень часто нам приходится сталкиваться с проблемой, как построить
складской комплекс с максимальной вместимостью и производительностью
на участке земли имеющем далеко не идеальную геометрическую форму
и множество ограничений: близко стоящие линии электропередач, другие
постройки, проходящие через участок муниципальные теплосети, канализации
и т.п. Решение каждой проблемы уникально. Ниже показаны некоторые
интересные примеры реализованных проектов.
При проектировании нового складского комплекса первоначально
был проведен анализ топологической съемки и визуальный осмотр участка
земли Заказчика.
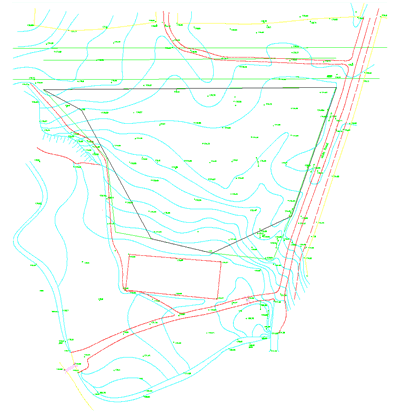
Рис.1 Границы участка земли Заказчика
Особенности этого участка - наличие только одной длинной стороны;
сильный уклон (перепад высот между верхними отметками и нижними
отметками на рисунке порядка 4 метров), наличие 2-х линий электропередач
рядом с верхней границей (дальняя с напряжением 110 кВ, ближняя
-220кВ) и возможность организации 1-го въезда с дороги для большегрузного
транспорта. В соответствии с межотраслевыми правилами по охране
труда строящийся объект должен находиться на расстоянии не менее
25 м от крайнего провода ЛЭП. В соответствии с правилами пожарной
безопасности вокруг здания должен быть организован кольцевой объезд
шириной не менее 6 метров. А при организации движения автотранспорта
необходимо учесть, что радиус поворота большегрузного автомобиля
равен 17 метрам. Исходя из этих факторов, было проработано несколько
вариантов пятна застройки. Согласованный с Заказчиком вариант показан
на рисунке 2.
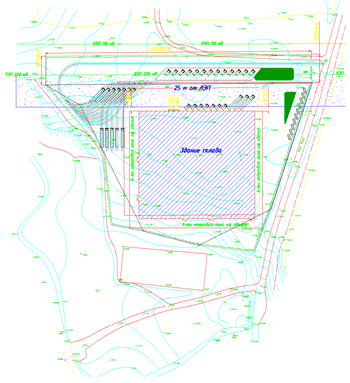
Рис.2 Схема согласованного участка.
Сравнивая рис.1 и рис.2, можно заметить, что первоначальной площади
участка не хватает для организации нормального движения автотранспорта.
Поэтому, Заказчику было предложено его расширить, используя для
этих целей землю, находящуюся в зоне линий электропередач для совершения
маневров.
Еще один интересный пример.
Основными факторами, определяющими полезную площадь склада, были
размеры маневровых площадок и расположение инженерных коммуникаций.
Ниже приведены варианты расположения маневровых площадок с вариантами
парковки автомобилей.
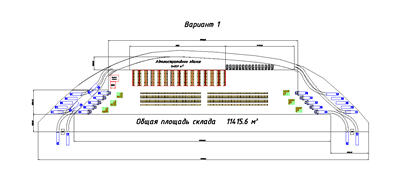
Данный вариант характерен тем, что машина, въезжая на территорию
складского комплекса, должна объехать здание терминала и осуществить
парковку на дальней от въезда рампе. Маневры машин показаны на рисунке.
Площадь, не занятую под маневровые площадки, используем под строительство
терминала (площадь терминала при данном варианте маневра составляет
11415,6 кв.м.).
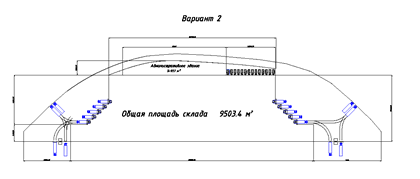
Второй вариант характерен тем, что машине, въезжая на территорию
складского комплекса, не надо объезжать здание терминала и осуществить
парковку на дальней от въезда рампе, а осуществлять парковку при
въезде. Маневры машин показаны на рисунке. Площадь, не занятую под
маневровые площадки, можно использовать под строительство терминала
(площадь терминала при данном варианте маневра составляет 9503,4
кв.м.).
Третий вариант характерен тем, что машина, въезжая на территорию
складского комплекса, должна объехать здание терминала и осуществить
парковку на дальней от въезда рампе. Отличительной особенностью
от первого варианта является тот факт, что парковка осуществляется
с поворотом задним ходом. Так же в этом варианте имеются две рампы
для приема длинномерных грузов. Есть высотная зона склада, в которой
предполагается работа высотных штабелеров. Маневры машин показаны
на рисунке. Площадь, не занятую под маневровые площадки, используем
под строительство терминала (площадь терминала при данном варианте
маневра составляет 13822 кв.м.).
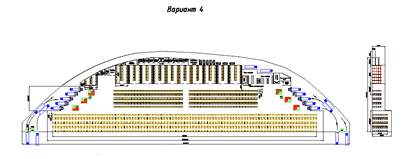
Четвертый вариант идентичен третьему, за исключением той особенности,
что рампы для приема длинномерных грузов были совмещены. Есть высотная
зона склада, в которой предполагается работа автоматических высотных
штабелеров. Маневры машин показаны на рисунке. Площадь, не занятую
под маневровые площадки, используем под строительство терминала
(площадь терминала при данном варианте расположения внутренних сооружений
составляет 13822 кв.м.).
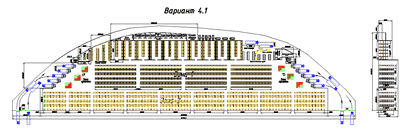
Вариант 4.1 идентичен четвертому, за исключением той особенности,
что на складе была выделена зона консолидации готовых заказов. Так
же в этом варианте пришлось отказаться от автоматической высотной
техники и использовать высотные штабелеры и комплектовщики на всей
территории терминала. Площадь терминала составляет 13881 кв.м.
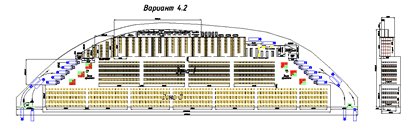
Вариант 4.2 так же идентичен четвертому, за исключением той особенности,
что на складе была несколько видоизменена разбивка стеллажей на
участки. Площадь терминала составляет 13881 кв.м.
Выбранный Заказчиком вариант планировочного решения (максимальная
площадь пятна застройки составила 13859 кв.м.), который приведен
ниже. При этом все инженерные системы
предполагается разместить под зданием склада.
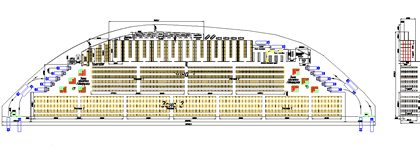
Б. Определение необходимых ресурсов и размеров функциональных
зон.
Оснащение современных складских комплексов необходимым оборудованием
и техникой требует значительных инвестиций. Действительно, стоимость
единицы современной складской техники в зависимости от назначения
и исполнения колеблется от 5000 до 80000 евро, стоимость одного
места хранения - от 20 до 200 евро. Сейчас многие инвесторы заказывают
проекты на универсальные складские комплексы с десятками тысяч мест
паллетного хранения, предназначенных для переработки громадных грузопотоков
и естественно, требующих множества единиц складской техники. При
этом могут применяться различные складские технологии, требующих
различных человеко-машинных ресурсов. То есть затраты на реализацию
проекта могут существенно отличаться. Как доказать эффективность
той или иной технологии и оптимизировать затраты инвестора?
Для ответа на эти вопросы в нашей компании используется имитационное
моделирование.
Некоторые виды решаемых задач:
1) определение количества человеко-машинных ресурсов, обеспечивающих
переработку
внешних (прием и отпуск) и внутренних (комплектация заказов, пополнение
ячеек
стеллажей, используемых для комплектации заказов) грузопотоков при
оптимальном уровне
их загрузки (то есть определение количества людей и необходимой
техники, выполняющих
требуемые технологические и подъемно-транспортные операции);
2) определение или уточнение технических характеристик машин (скоростей
рабочих движений)
для обслуживания необходимых грузопотоков;
3) определение количества человеко-машинных ресурсов, обеспечивающих
переработку
грузопотоков при заданных временных порогах обслуживания клиентов;
4) определение необходимой площади для зон приемки, сортировки,
комплектации и хранения
грузов;
5) определение количества мест парковки на территории склада для
транспорта, реализующего
внешние грузопотоки, и рационально количества мест парковки непосредственно
к грузовой
рампе;
6) определение необходимого количества ворот в складском помещении;
7) проверка эффективности использования различных вариантов компоновочных
решений для
хранения груза и сборки заказов
8) определение наиболее эффективных алгоритмов управления грузопотоками;
9) определение наиболее эффективных расписаний выполнения различных
работ;
10) определение уровня складских запасов системы (в том числе иерархически
организованной) с
учетом параметров поставок и возможного спроса.
Определение необходимых ресурсов, обеспечивающих заданные
временные пороги обслуживания клиентов.
При разработке проекта нового складского комплекса площадью 20000
м2 была поставлена задача по оптимизации человеко-машинных ресурсов
обеспечивающих, заданные временные пороги обслуживания клиентов
типа «самовывоз». Один из результатов анализа, проведенного с помощью
имитационного моделирования, показан на графике зависимости времени
обслуживания клиентов при использовании 8 погрузчиков от числа сборщиков.
Как видно из рисунка, при использовании заданных диапазонов трудоемкости
сборки заказа и при вывозе заказа на рампу обслуживание клиентов
может быть осуществлено :
1) за 30 минут с помощью 3 сборщиков и 8 погрузчиков;
2) за 15 минут с помощью 5-6 сборщиков и 8 по грузчиков;
3) около 10 минут с помощью 12 сборщиков и 8 погрузчиков;
4) дальнейшее увеличение числа сборщиков не приводит к улучшению
результата.
Получение такого решения кроме как путем проведения вычислительных
экспериментов на зависимость времени обслуживания клиентов (самовывоз)
от количества сборщиков при использовании на складе 8 погрузчиков
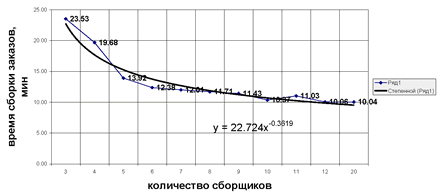
имитационной модели просто невозможно, так как на складе существует
множество грузопотоков, а одни и те же погрузчики участвуют при
выполнении различных операций.
В. Максимизация использования площади склада.
Для многих успешно развивающихся предприятий, постоянно наращивающих
свой грузооборот, но имеющих ограниченные складские площади, возникают
естественные вопросы - каковы предельные возможности грузопереработки
на этом складе? Каким образом надо произвести реконструкцию, чтобы
максимально использовать площадь, на которой производятся основные
складские операции? Когда необходимо принять решение о строительстве
нового склада, соответствующего требованиям фирмы и лишенного недостатков
существующего?
Чтобы ответить на эти вопросы необходимо грамотно решить задачу
об организации хранения и отбора грузов. Наиболее сложный, но весьма
распространенный случай - разработка технологии грузопереработки
для склада многономенклатурных грузов. При этом грузы могу иметь
большие разбросы значений частот спроса, количества вложений, геометрических
размеров и весовым характеристикам.
Одна из основных задач складского комплекса -комплектация и отпуск
заказов клиентам. При этом практически на всех предприятиях товар
может отпускаться паллетами, коробками и более мелкими вложениями
(штуками). Таким образом, на складе должны быть места хранения для
паллет и коробок и штук. С другой стороны должен быть организован
паллетный, коробочный и штучный отбор. Паллетный отбор особых трудностей
при наличии системы оперативного управления складом не вызывает
и может осуществляться из любых ячеек стеллажей с помощью штабелирующей
техники.
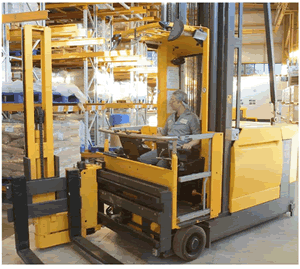
Однако коробочный и штучный при значительном ассортименте товаров
без применения специальной техники рационально организовать весьма
не просто. Дело в том, что любой товар должен находится в зоне прямого
доступа комплектовщика - обычно 1 ярус паллетных стеллажей. То есть
возникает высокий спрос на места на 1 ярусе. Проблема еще более
усугубляется в случае наличия крупногабаритных и тяжелых товаров.
С другой стороны существует естественное стремление сократить путь
перемещения комплектовщика. Возникает конфликтная ситуация -организация
коробочного и штучного отбора влечет за собой увеличение потребности
в местах на нижнем ярусе стеллажей, а это - увеличение длины фронта
отбора. Можно для сокращения длины фронта организовать отдельные
зоны для коробочного и для штучного отбора. Однако во всех этих
случаях значительно возрастает площадь склада, а его объем используется
неэффективно.
Какой может быть выход из этого положения?
1) Применение специальной подъемно-транспортной техники. Например
являясь эксклюзивным представителем компании АТЛЕТ (Швеция), мы
производит поставку узкопроходных комплектовщиков с высоких уровней.
Использование такой техники позволит убрать отбор коробками с нижних
ярусов стеллажей и обеспечить наиболее полное использование объема
склада.
2) Специалисты департамента складских технологий нашей компании
разработали оригинальные алгоритмы по определению мест отбора и
мест хранения для различных групп товаров и сокращению длины фронта
отбора. При этом учитываются все характеристики грузов и
определяется необходимая ориентация при размещении грузов на стеллажах.
Все это обеспечит наиболее эффективное складских площадей, сокращение
времени обслуживания клиентов и снижение инвестиций в строительство
и оснащение складского комплекса.
Г. Определение структуры склада и типов оборудования.
Хочется отметить, что уникальность создаваемых складских систем
часто вытекает из того набора технологических операций, которые
необходимо осуществлять с грузом на складе. Особенно много специфических
моментов приходится учитывать при создании складов для хранения
свежих овощей и фруктов. Действительно на таких складах, кроме выполнения
чисто складских операций (приемка, хранение, комплектация) для подготовки
товаров к реализации необходимо проводить фасовку различных продуктов
в разные виды упаковок: например, ягоды — на подложки или в пластиковые
контейнеры; цитрусовые, яблоки и корнеплоды — в сетки. Кроме того,
такие продукты как банан требуют особой операции - «дозаривания»
(дозревания) в специальных камерах. В результате на складе появляется
соответствующее оборудование и возникает множество дополнительных
грузопотоков и особых функциональных зон. На мировом рынке сегодня
реализуется примерно 140 видов фруктов и 100 видов овощей. Однако
среди них много необычной на вид и непривычной на вкус «экзотики»,
и в нашей стране устойчивым спросом пользуются всего около двух
десятков видов, причем для них характерны большие суточные объемы
приходов и отгрузок, значительные запасы хранения. Следовательно,
для наиболее ходовых товаров можно ,в принципе, использовать набивные
стеллажи типа «drive in». Вместе с тем, применение подобных стеллажей,
лишает продавца гибкости, так как каждые сутки он обязан отгружать
и принимать товары целыми секциями. Учитывая, подобное обстоятельство
можно предложить использование специальной техники, обеспечивающей
размещение паллет на двойную глубину.
Анализ результатов, полученных при разработке проекта для крупной
международной оказалось, что в случае использования специальной
техники для размещения грузов на двойную глубину при значительном
увеличении гибкости эффективность использования площади склада практически
не уменьшилась по сравнению с набивными стеллажами.